Manufacturing remains a huge industry in the United States and around the world. And, in the past year to 18 months, the manufacturing industry has experienced a pair of industry-rattling trends that are decidedly different.
First, manufacturing companies have gained access to the most advanced technologies ever available in the industry. These technologies have the power to transform operations, reducing lead times and improving both quality and revenue. But, at the same time, the COVID-19 pandemic has placed a significant strain on day-to-day operations. There are manufacturing companies and clients that no longer exist in 2021 due to the challenges related to the pandemic that dominated the world in 2020.
As the pandemic subsides and advanced technologies remain available to manufacturing companies, now is an ideal time to return to strategic manufacturing planning exercises. What will 2021 hold in store for your business? Only a solid plan can help you determine where you want to go and how your company can get there.
Here’s a look at the different stages of manufacturing planning, as well as 7 trends that strategic plans should address in 2021.
The 3 Stages Of Strategic Manufacturing Planning
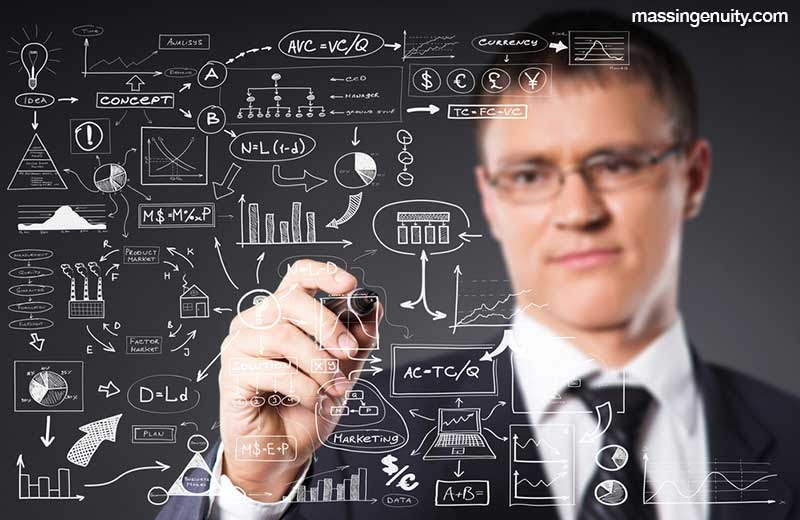
Strategic planning in the manufacturing industry should start with a simple framework. Break the planning work up into these 3 basic phases:
- Create an Agenda: What direction will guide your firm? Again, this question may be more relevant in 2021 than in years past given the changes that may have taken place in your business over the past 18 months.
- Outline Desired Results: What specific, measurable results should your company’s direction drive toward?
- Implement the Plan: Implement the strategic plan in such a way that you track and measure real-world outcomes against the desired results.
Of course, each of these phases will include a great deal of debate among firm decision-makers and an enormous amount of detail as your company chooses a direction, settles on desired results, and then implements its plan.
What Should Your 2021-22 Plan Address?
As we collectively emerge from the COVID-19 pandemic, your manufacturing company is likely taking a forward-looking posture and searching for competitive advantages. To ensure that your firm positions itself for success in 2021 and beyond, consider the following 7 trends as you piece together a strategic plan.
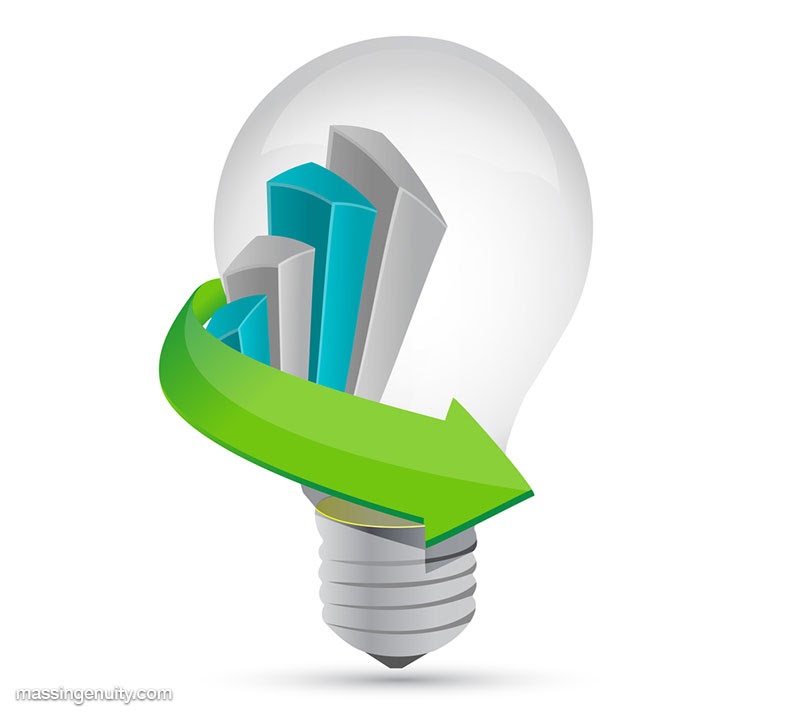
1. The Pivot From Covid-19
Not all manufacturing companies can simply go back to the way things used to be in a post-COVID-19 world
As noted above, some manufacturing companies didn’t make it out of the pandemic, and almost all manufacturing companies likely have a client that didn’t survive 2020.
But how will your manufacturing business respond to the realities of 2021? Gartner has provided a series of insights into how businesses across industries are handling the COVID-19 pandemic. In 2020, we went through the “respond” and “recover” phases, wherein companies took immediate action to keep workers safe and then restarted and scaled activities.
We’re now entering a third phase — “renew.” During the renewal phase, companies will have to create new foundations for their businesses. These new foundations should be designed to achieve one of the following 5 outcomes:
- Retire: Businesses may determine there’s no path forward and begin plans to retire operations altogether.
- Reduce: Businesses may find that new realities will force them to operate at lower capacity for the foreseeable future.
- Return: Business may discover that they can return to operations in much the same way they approached them before COVID-19.
- Reinvent: Businesses may grow by creating new business lines.
- Rescale: Businesses may embrace changes from the pandemic in such a way that operations boom and scale to heights previously unknown.
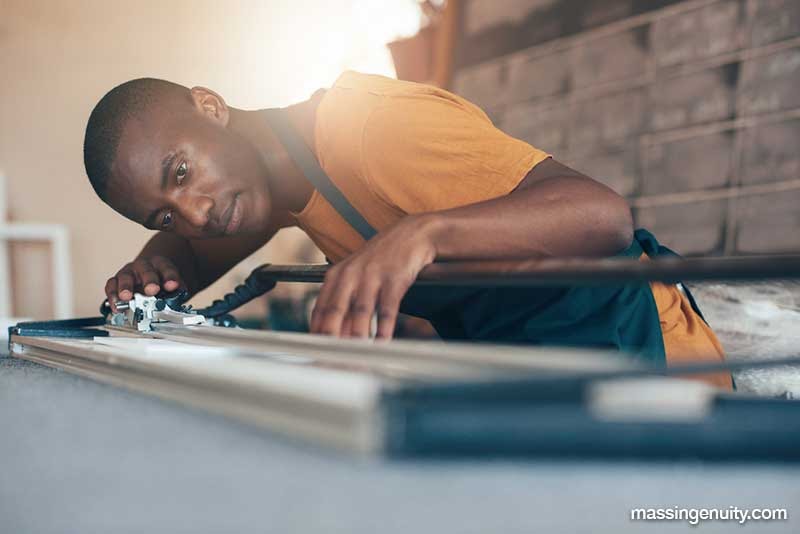
2. Predictive Maintenance
There’s nothing new about preventative maintenance in the manufacturing industry, but it continues to be an important consideration for firms around the world.
Downtime happens. But extended downtime of even an hour or longer can start costing manufacturing companies lots of money. Depreciation happens, too. Over time, your equipment gets older and less effective, reducing your company’s productivity. The cost of replacing equipment often represents a serious investment that requires significant planning.
But preventative maintenance helps on both fronts — reducing downtime and extending any piece of equipment’s lifespan.
The good news is that it’s easier than ever to execute preventative maintenance plans due to the manufacturing-related technologies now available. When you find the right manufacturing technologies and combine them with high-quality enterprise performance software, you’ll be able to anticipate maintenance needs better than ever, reducing downtime and saving your business real money.
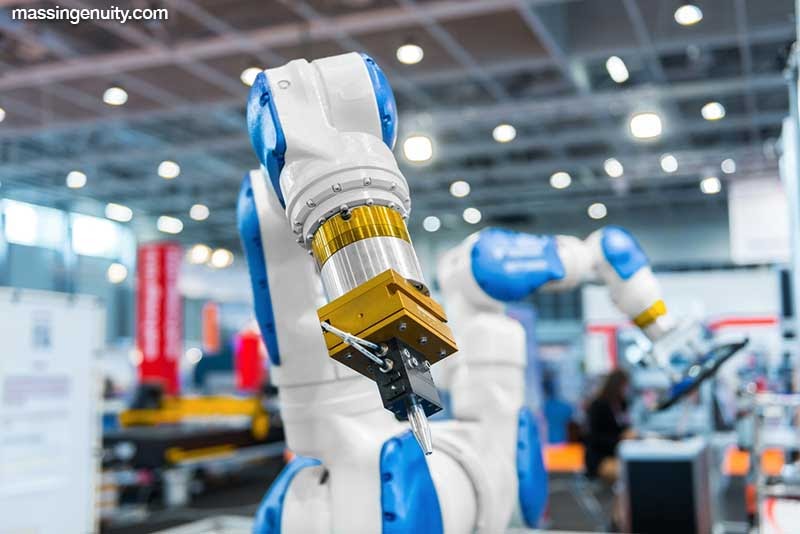
3. The Internet of Things (IoT)
What technologies are powering preventative maintenance? Let’s start with the manufacturing Internet of Things — sometimes known as IoT.
The IoT is a term for “smart” equipment and tools that manufacturing companies are now quickly adopting and introducing in their plants. These pieces of equipment and tools are designed for connectivity, which means enhanced remote monitoring capabilities that make preventative maintenance programs easier to implement.
The collective move toward “smart” factories, plants, and manufacturing sites is known as Industry 4.0. If your manufacturing business is not making Industry 4.0 a key consideration during strategic planning, it will have a hard time competing in the manufacturing future that is rapidly approaching.
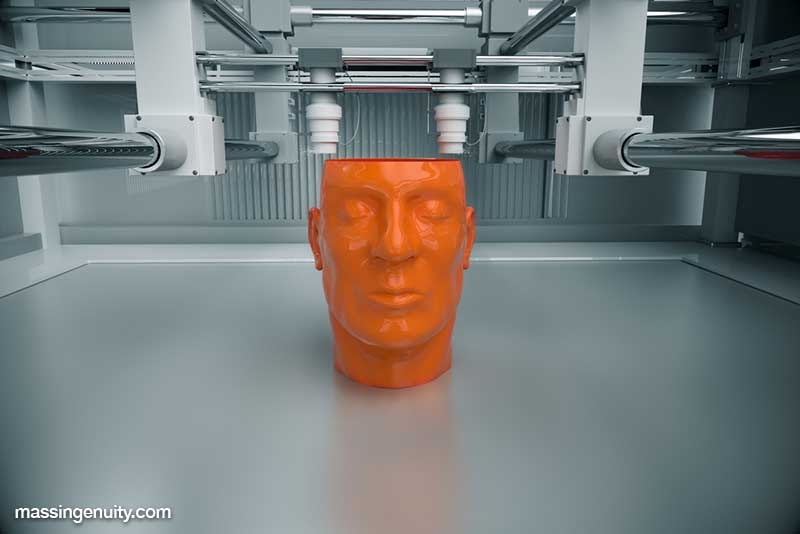
4. 3D Printing
3D printing is empowering preventative maintenance, not from an anticipation standpoint, but rather from an execution standpoint.
At many plants, it can be incredibly difficult to find factory-issued replacement parts for equipment that’s been in use for decades. 3D printing, also known as “additive technology,” allows operators to quickly create the small replacement parts needed to properly maintain equipment and generally reduce downtime.
The trends on this list can also work in tandem. For example, the IoT can help you identify emerging maintenance issues. And then 3D printing can help you quickly fabricate a replacement part without the need to look for a supplier.
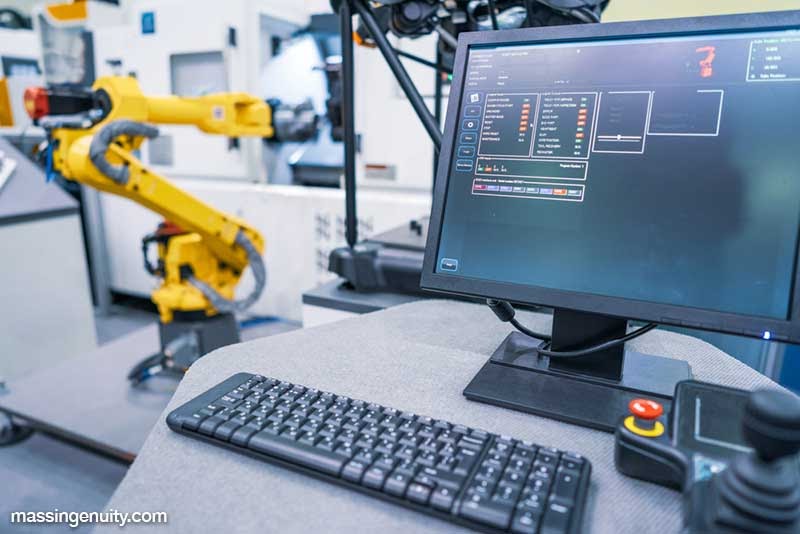
5. Augmented Reality
Augmented reality also helps with preventative maintenance — again, from an execution standpoint.
In many cases, factories use augmented reality to overlay digital schematics and instructions atop real machines. This digital content is used to guide operators through simple maintenance and repair tasks. Where previously operators relied on their own experience or hard-copy guides to know how to perform these maintenance and repair tasks, augmented reality accelerates the time needed to complete these tasks — and increases the effectiveness of the operators conducting the maintenance or repairs.
6. Pilot Plants
New manufacturing technologies should be introduced to factories and plants as part of a careful, deliberate process. Many manufacturing companies are now using pilot plants to test out new technologies before implementing them throughout an entire company or network of different sites.
Any manufacturing company wants to reduce risk — the risk of downtime, the risk of poor quality, the risk of safety threats to workers, etc. These risks aren’t present with all-new manufacturing technologies — but pilot plants help reduce any risk by providing smaller, more stable environments for testing. If new technologies thrive within pilot plants both from safety and effectiveness standpoints, it’s safe to distribute them more broadly.
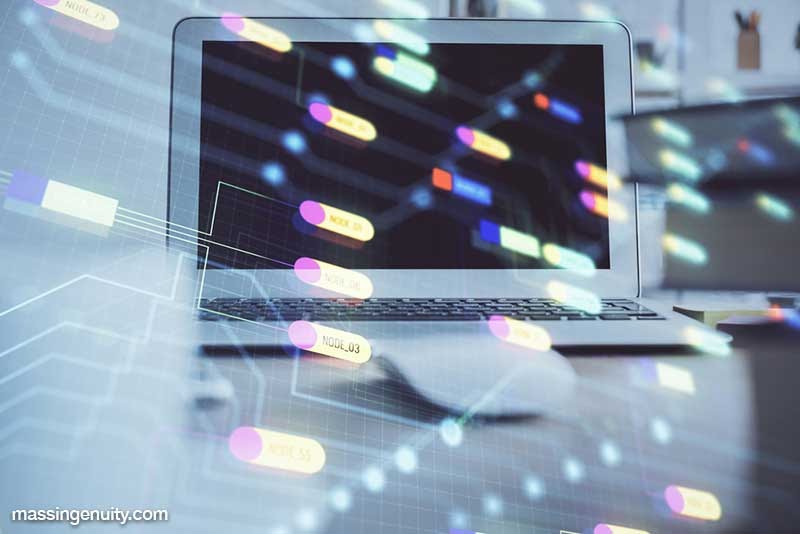
7. Big Data
You may hear the term “big data” thrown around as an elusive concept with fuzzy real-world implications.
But manufacturing companies are in a unique position to take advantage of big data, leveraging information to make plants more efficient, more effective, and safer.
But there’s a natural barrier to using big data — gathering data is easy, but properly analyzing and drawing insights from that data is far more difficult. Manufacturing companies really need enterprise performance software that can help them from the data gathering phase to the phase of analysis and drawing insights from that data.
The Challenge: Tracking Your Plan’s Effectiveness
How can your business best gather, analyze and draw insights from performance-related data? At Mass Ingenuity, we offer Results Software that simplifies and streamlines the data process — guiding you from collection to analysis and clear conclusions.
When you try to manage enterprise performance management data on your own, the time you invest in strategic planning leads to poor follow-through and a serious lack of accountability. But, when you choose an enterprise performance management tool like Results Software, you get the visibility you’ve always wanted into your business — plus data to analyze and draw conclusions from at your fingertips.
Start taking advantage of data available to your manufacturing company when you get in touch to schedule a demo of Results Software